氨氮是一种营养性污染物,它在水体中的过量存在会对生物及其生存环境造成严重危害。因此,工业废水排放之前的脱氨工作尤为重要。氨氮废水的处理技术[1]主要有: 选择性离子交换法[2]、生物脱氮法[3,4]、吹脱法[5]、折点加氯法[6]、化学沉淀法[7]、催化湿式氧化法[8]、膜法[9]、电渗析法[10]和蒸气气提法[11]等。以上废水氨氮脱除的方法各有优点,也存在一定的缺点和应用局限,如处理成本高,条件控制严格,易造成二次污染等[12]。膜脱氨技术是一种更加有效的接触传质过程,其中有代表性的主要有VMD[13,14]及MA[15,16]等过程。VMD 与MA 脱氨均是膜蒸馏脱氨的2 种形式。VMD 是利用真空技术使膜界面形成氨分压差从而达到脱氨目的; MA 脱氨是利用酸性溶液作吸收剂,其快速的化学反应使界面氨分压差增大明显,具有较高的脱氨效率。
脱氨效率与起始氨氮浓度、温度、真空度、pH、脱氨时间及膜性能等有直接的关系。VMD 过程脱氨效率不高,脱氨后废水难以达到排放或回用标准,但其脱除的氨可回收制成氨水回用于工业生产,从而可以降低含氨废水处理成本。故VMD 可以用于高浓氨氮废水的初步脱氨。
相对VMD 而言,MA 脱氨过程脱氨效率较高,但膜吸收脱氨后形成的硫酸铵、氯化铵等副产物,由于浓度低,pH 值低不能直接作为肥料加以利用,需要解决废吸收液的回收问题。
若将VMD 和MA 结合起来,有望实现高氨氮废水的高效脱氨并解决废吸收液的二次处置难题。本文在实验室规模下对VMD 和MA 脱除水溶液中的氨氮进行了研究,并建立了一套全新的高效处理高氨氮废水的集成膜工艺体系。
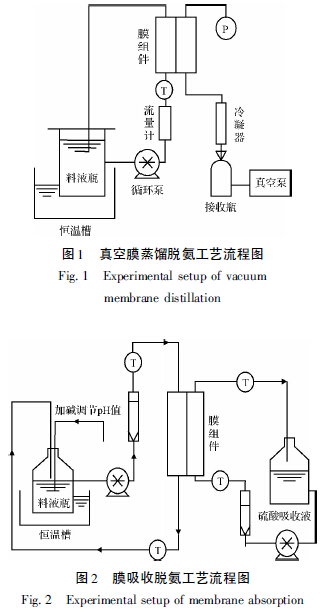
1 实验
1.1 实验材料与仪器
实验用pp 中空纤维膜组件采用美国MEMBRANA公司的Liqui-cel? MiniModule,膜基本参数为孔径0. 2 μm,孔隙率40%,内径220 nm,外径300nm,有效膜面积0. 18 m2。
实验仪器: SHB-IV 水循环真空泵,巩义市予华仪器有限责任公司; FE20 实验室pH 计,梅特勒-托利多仪器(上海) 有限公司; JM624U 电子温度计,天津今明仪器有限公司。
模拟废水和调节模拟废水pH 值的碱溶液分别由氯化铵、氢氧化钠(分析纯,国药集团化学试剂有限公司) 与去离子水配制而成。
1.2 实验装置与方法
本研究采用真空膜蒸馏实验装置和直接接触式膜吸收装置。如图1 所示VMD 工艺流程,热循环始于料液,料液被泵入恒温槽升温后经过流量计和温度计,流经膜组件后返回料液瓶; 冷侧则由真空泵将透过膜孔的挥发态氨抽出并冷凝回收。
如图2 所示MA 工艺流程,料液通过恒温水浴加热,泵入中空膜组件的内侧,产水和过膜氨分子被稀硫酸吸收液吸收,通过磁力循环泵实现膜吸收两侧的循环。膜组件的两侧进出口装有温度计记录料液和吸收液进出口温度,冷侧和热侧流速测定采用转子流量计记录和控制。
1.3 分析方法
料液为分析纯NH4Cl 与去离子水配制而成,每次配制料液1. 5 L。设定条件运行脱氨过程,每隔一定时间从料液槽中取样并测试分析其中氨氮的浓度,通过纳氏试剂比色法检测不同时刻料液中NH3-N 浓度来绘制ln(C0 /Ct) -t 图,根据公式(1) 和(2)求出氨的去除率和传质系数。
R = (C0-Ct)/C0 ×100% (1)
式中: C0为氨的初始浓度(mg /L) ; Ct为t 时刻剩余氨的浓度(mg /L) 。
ln(C0/Ct) = KAt/V (2)
式中: C0和Ct分别是溶液中氨的起始浓度和t 时刻的瞬时浓度(mg /L) ; K 为氨的传质系数(m/s) ; A 为膜有效面积(m2 ) ; V 为氨溶液体积(L) 。
2 结果与讨论
2.1 料液pH 的影响
配制浓度为1 000 mg /L 的料液,控制循环流速0. 10 m/s,进口温度40℃,真空度- 90 kPa,调节料液pH 分别为9. 5、10. 0、10. 5 和11. 0 进行VMD 实验,结果如图3 所示。
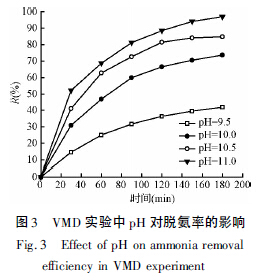
配制浓度为1 000 mg /L 的料液,控制两侧循环流速都为0. 10 m/s,料液进口温度40℃,稀硫酸吸收液进口温度20℃,浓度0. 02 mol /L,调节料液pH分别为9. 50、10. 0、10. 5 和11. 0 进行MA 实验,结果如图4 所示。
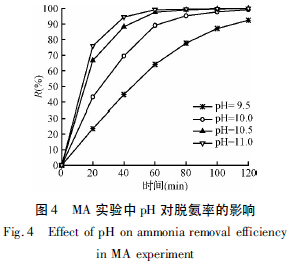
由图3 和图4 都可以明显看出,料液pH 值越大,脱氨效率越高,脱氨速度越快。VMD 实验中,pH = 11.0 时,在系统运行3 h 后脱氨效率达到96. 9%,pH = 10. 5 时,3h 后达到84. 9%。但pH =9. 5 时脱氨率明显减弱,因为在氨氮溶液体系中,pH等于9. 25 时[NH +4]∶[NH3]= 1∶ 1[17],由此,体系中[NH3]所占比例越大,脱除效率越高,所以料液pH值对脱氨率的影响很大。理论上,料液pH 值越高越有利于氨的脱除,但过高pH 会导致调节pH 时耗碱过多并且产生过高碱度的二次废水,建议VMD脱氨实验料液pH 值设置在10. 0 左右,可以在产生二次污染风险较小的情况下保证较高的脱除率。MA 实验中,pH 的影响主要表现在脱氨速度上,pH= 11. 0 时,在系统运行1 h 后就达到了99% 的脱氨效率,pH = 10. 5 时,2 h 脱氨效率达99. 9%。pH =9. 5 脱氨速度相对显弱,但2 h 后也达到了92. 4%的效率。
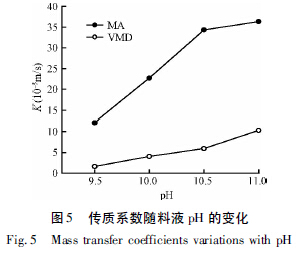
如图5 所示,pH 值对VMD 和MA 实验的传质系数影响很大,K 值先开始迅速提高后又趋于缓慢增加,随着pH 由9.50 增大到11.0,2个膜过程的K值分别由1. 64 × 10-5 m/s、12.11 × 10-5 m/s 升高到了10.33 × 10-5 m/s、36.33 × 10-5 m/s,分别提高到初始K 值的6.3 倍和3.0 倍。这种现象可以通过NH3在水溶液中的电离平衡解释,提高溶液的pH值,OH-浓度增大,平衡方程h2o向右移动,生成的氨气越多,从而提高了膜两侧的蒸气压差,提高了传质动力,导致K 值增大。
2.2 料液进口温度的影响
配制浓度为1 000 mg /L、pH 为10. 5 的料液,控制循环流速0. 10 m/s,真空度-90 kPa,调节料液进口温度分别为20、30、40 和50℃进行VMD 实验,结果如图6 所示。
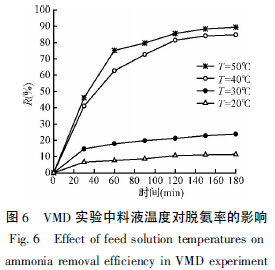
料液进口温度对VMD 脱氨实验过程的影响很显著,随着温度的增加,脱氨速度和效率明显提高,当温度设置在20℃和30℃时脱氨效率较低。在料液进口温度达到40℃时,VMD 脱氨效率明显提高,料液进口温度调节到50℃脱氨效率进一步提高,但过高初始料液温度会导致整个工艺能耗大大增加。
配制浓度为1 000 mg /L、pH 为10. 5 的料液,控制两侧循环流速都为0.10 m/s,稀硫酸吸收液进口温度20℃,浓度0. 02 mol /L,调节料液进口温度分别为20、30、40 和50℃进行MA 实验,结果如图7 所示。
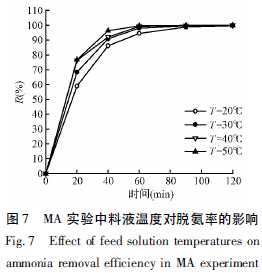
相对VMD 过程来说,温度对MA 脱氨过程的影响很小,随温度增加,脱氨速度有缓慢增加的趋势,但是对比较终脱氨效率没有太大的影响,2 h 后都达到99. 9%甚至以上的脱除率。
由图8 可知,在料液进口温度为20 ~50℃条件下,VMD 方法脱氨时,料液进口温度对传质系数K的影响很大,随料液进口温度由20℃增加至50℃,VMD 实验中氨的传质系数由0.33 × 10-5 m/s 提高到5.72 × 10-5 m/s。这是由于温度的上升,挥发性物质氨的蒸气分压明显增加,提高了传质推动力。而在MA 实验中,温度的影响没有对VMD 实验的影响显著,由20℃时K 值为26. 56 × 10-5 m/s 提高到50℃时的K 值为35.67 × 10-5 m/s,仅提高了34%。
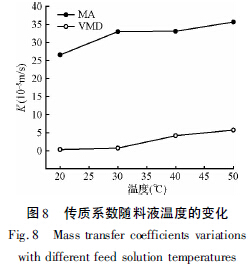
3 VMD 和MA 集成脱氨工艺
3.1 集成工艺流程
充分考虑VMD 与MA 脱氨工艺的优缺点,构建了VMD-MA 集成膜脱氨系统,工艺流程图如图9所示。
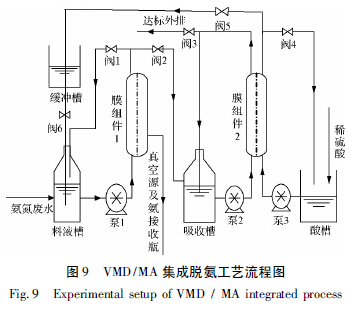
含氨废水预先用0. 2 mol /L 的NaOH 溶液调节pH 至10. 5 后引入真空脱氨料液槽中,由真空脱氨循环泵1 泵入PP 脱气膜组件1 的内侧,脱氨后返回料液槽,当脱氨效率达到80% 以上时关闭阀门1 开启阀门2 将VMD 处理后的料液引入MA 吸收槽中。重新调整pH 为10.5 后泵入PP 脱气膜组件2 内侧进行膜吸收脱氨后返回吸收槽,直到脱除效率达到目的值时,开启阀门3,调节pH 为中性后达标外排。酸循环槽内起始浓度为0. 02 mol /L 的稀硫酸吸收剂被泵入PP 脱气膜组件2 的膜外侧,带走过膜氨分子回到酸槽,生成硫酸铵。当稀硫酸吸收剂pH 大于4 时开启阀门5 关闭阀门4,将硫酸铵溶液引入吸收剂缓冲槽,调节至所需pH 后开启阀门6 流入真空脱氨料液循环槽中与含氨废水混合继续脱氨。在脱气膜组件1 中膜另一侧接氨回收真空系统为VMD 工艺提供动力,由膜组件1 脱除的氨被氨接收瓶冷凝接收。
3.2 集成工艺脱氨实验
配制4 种不同浓度1 000、3 000、6 000 和10 000 mg /L的氨氮初始料液各1 L进行膜工艺集成实验,结果如图10 所示。
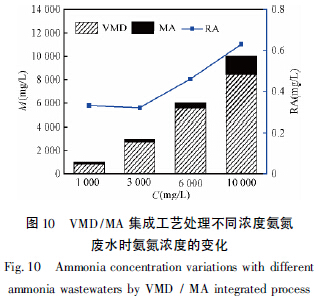
由图10 可知,在VMD 操作条件为: pH = 10.5,T料液= 40℃,v料液= 0.10 m/s,p =-90 kPa,MA 操作条件为: pH = 10.5,T料液= 20℃,T硫酸= 20℃;v料液= 0.10 m/s,v硫酸= 0.10 m/s,H2SO4 0.02 mol /L。不同初始浓度的氨氮废水在经过预处理之后进入VMD/MA 集成膜处理工艺,先由VMD 工艺分别脱除84. 85%、90. 46%、92. 98% 和84. 43% 的氨氮,接着进入MA 工艺脱除剩余氨氮的99. 78%、99. 89%、99.89%和99. 96%,这样经过VMD 和MA2 个工艺之后废水中残留的氨氮浓度(RA) 就是图中折线所示,分别为0. 33、0. 32、0. 46 和0. 63 mg /L。根据《污水综合排放标准-GB8978-1996》,第二类污染物比较高允许排放浓度,医药原料、染料、石油化工工业氨氮排放量一级标准≤15 mg /L、二级标准≤50mg /L; 其他排污单位氨氮排放量一级标准≤15 mg /L、二级标准≤25 mg /L。出水符合污水综合排放标准一级标准。具体参见http://www.dowater.com更多相关技术文档。
4 结论
本研究分别对VMD 和MA 实验过程中料液pH和料液进口温度2 个重要操作条件对脱氨率的影响做了分析,并将VMD 技术和MA 技术集成进行高效脱氨,得到如下结论:
(1) VMD 工艺在pH =10.5,T料液= 40℃,v 料液=0.10 m/s,真空度=-90 kPa 操作条件下脱氨率可达85%,MA 工艺在pH = 10. 5,T料液= 20℃,T硫酸=20℃,v料液= 0. 10 m/s,v硫酸= 0. 10 m/s 条件下脱氨率可达99. 6%。综合经济和效率方面考虑,集成工艺操作参数也设为上述数值。
(2) 在实验涉及的操作条件范围内,料液pH 和进口温度对VMD 脱氨效果的影响较大,提高料液pH 和进口温度可以明显提高VMD 的脱氨效率。MA 实验中,料液pH 对的脱氨效率影响比较显著,料液进口温度的影响不大。
(3) VMD/MA 集成脱氨工艺处理不同浓度高氨氮废水效率可达99. 96% 以上,出水符合污水综合排放标准一级标准。
本集成工艺结合了VMD 和MA 工艺在脱氨实验中的优点,可以回收利用氨并且将硫酸铵废液回流继续脱氨从而解决硫酸铵的二次污染问题。为高浓度氨氮废水的经济有效处理提供了一条全新技术路线。
中天恒远厂家直销!优惠的价格!周到的服务!
水处理产品咨询热线:010-8022-5898 186-1009-4262